First, increase the contrast of full-color LED displays. Contrast is one of the key factors affecting the visual effect. In general, the higher the contrast, the clearer the image is and the brighter the color is. High contrast is very helpful for image clarity, detail performance, and grayscale performance.
Second, improve the gray level of full-color LED display. Gray scale refers to the brightness level of the single primary color brightness of the full-color LED display screen that can be distinguished from the darkest to the brightest. The higher the gray level of the full-color LED display, the richer the color, the brighter the color; , display a single color, simple changes. The increase in gray level can greatly increase the color depth, so that the display level of the image color increases geometrically.
Finally, reduce the dot spacing of full-color LED displays. Reducing the dot pitch of a full-color LED display can improve its sharpness. The smaller the dot pitch of a full-color LED display, the finer the screen display.
Die Casting Parts:
The casting is a metal human control of hot working process relatively early, has a history of about 6000 years.In early 1700 BC to 1000 China has entered into casting heyday era,the technology has reached a very high level.
the material to be casting is usually solid but heated to a liquid metal (copper, iron, aluminum, lead, tin, etc.), and mold materials can be sand, metal and even ceramics. In response to different requirements, the use of the method will be different.
Different Category:
Casting blank is almost forming, which achieves the goal of free machining or less processing, reduces cost and reduces production time to a certain extent. Casting is one of the basic processes in modern equipment manufacturing industry.
(1) Sand casting:
Using sand as the mold material, also known as sand casting, foundry, including wet sand, dry sand and chemical hardening sand 3, but not all are available in sand casting. Advantage is low cost, because of the use of the mold sand can be reused; drawback is the mold manufacture time-consuming, repeated use casting model is not possible. To damage can be achieved after the finished product.
(2) Special Casting Process:
According to the special casting molding materials can be divided into natural mineral sand as the main materials (such as casting, mud casting, shell casting, vacuum casting, mold casting, ceramic mold casting, special casting and metal) as the main cast materials (such as metal casting, pressure die casting, continuous casting, low pressure casting, centrifugal casting, etc.
2.1 Metal mold casting method: using high melting point is the raw material made of metal mold. The subdivision for gravity casting, low pressure casting and pressure casting method. By casting the melting point can be cast metal has also been limited.
2.2 Lost wax casting method: this method can for membrane casting and solid casting. First the object copy the required casting wax, and then dipped into ceramic containing (or silica sol) in the pool and stay dry, the wax replica covered with a layer of ceramic membrane, repeating the steps until the outer membrane is sufficient to support the casting process (about 1/4 inch 1/8 inch), wax melting in the mold, and out of the mould. Then many times to enhance the mold temperature, the hardness can be used to rear casting.
Based on different casting raw material,we`ve Steel Die Casting,copper alloy die casting and aluminium alloy die casting.
Processing:
(1)The mold preparation (liquid metal become a solid container for casting ) according to the material used can be divided into sand, metal, ceramic, clay, graphite, according to the frequency of use can be divided into single type, semi permanent and permanent mold preparation, quality is the main factor affecting the quality of castings;
(2) The melting and casting;:casting metal (alloy) mainly include all kinds of cast iron, cast steel and casting of nonferrous metal and alloy castings;
(3) The processing and inspection: casting processing including removal of the core and the casting surface removal of foreign body, riser, shovel thorn and sanding fash protrusions and heat treatment, plastic. Anti rust and rough machining.
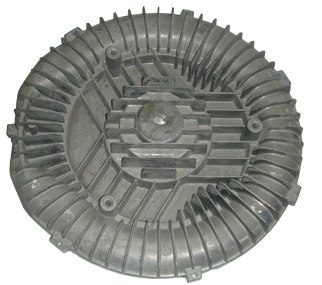
Die Casting Parts,Steel Die Casting,Copper Die Casting,Aluminium Die Casting
VESTA Motoring Ltd , https://www.vesta-industry.com