Huaneng Shang'an Power Plant No. 1~#4 all adopt direct-fired coal feeding method, and the selected coal feeder is Model 8404 Weighing Coal Feeder with electronic weighing device and microprocessor controller manufactured by STOCK, USA. Machine, the drive device is a slip speed motor.
First, the existing problems (1) slip speed motor is to adjust the electromagnetic slip clutch coil excitation coil current to achieve speed control function, in which the speed excitation coil current loss of heat converted and the clutch master and slave rotor The heat generated by coupling in a magnetic field is cooled by natural wind. Due to the large dust in its operating environment, the air gaps between the clutch master and slave rotors are filled with ash. This can easily cause the slip motor to fail to adjust speed or fail to regulate speed. The amount of coal fluctuates greatly, causing it to be forced out of operation.
(2) The input speed feedback of the gearbox of the coal feeder is provided by the AC tachometer generator installed on the output shaft of the electromagnetic slip clutch. The magnetic rotor of the AC tachometer generator is easily damaged due to the material being brittle, resulting in The velocity feedback disappeared, the coal feeder tripped, and even the robbed coal machine jumped, thereby threatening the safe and stable operation of the unit.
According to incomplete statistics, Huaneng Shang'an Power Plant's Phase 1 2×350MW unit has been put into production since 1989. During the operation, the slippage of the 2×350MW unit has failed and the speed feedback has failed. As a result, the coal feeder has tripped and even jumped to the coal mill for more than 10 times.
Second, the 8424 type electronic weighing coal feeder control principle STOCK Corporation 8424 electronic weighing coal feeder control block diagram shown in Figure 1. The function of the power board is to convert the DC power of the user (DCS) to a low voltage stable DC power supply required for operating the electronic control equipment. The AC power is converted by the transformer into a series of low voltage power, and then is rectified, filtered and stabilized to supply the electronic power. Circuit use.
The input/output circuit is located on the power board, and the opto-isolator isolates the microprocessor from the factory electrical control system to eliminate transients or noise disturbances. The input signal conversion board and the frequency/current conversion board (F/I) are inserted on the power board, where the input signal conversion board converts the user's fuel demand signal into a normal 0 to 10 kHz frequency signal for use with the microprocessor. System connection; frequency/current conversion board (F/I) converts the speed feedback digital signal output by the microprocessor to a 4-20 mA current signal and returns it to the user (DCS) for use.
When the microcomputer control board receives the coal feeding rate request signal provided by the user (DCS) through the input signal conversion board, it measures the weighing signal and calculates and sends a speed control signal (30 to 1500 Hz/10 VDC) to the motor speed control board. . The motor speed control board can control the speed of the motor by controlling the amount of current that is input to the slip ring of the slip speed regulating motor, thereby driving the slip speed regulating motor to rotate to achieve the required speed.
The speed feedback of the slip speed regulating motor is a pulse signal sent from the AC tachometer generator installed on the output shaft of the clutch. All the way back to the summing point of the error amplifier of the motor speed control board, where the input signal is compared, the error amplifier to adjust the electromagnetic clutch coil current, to maximize the correction of the speed error, forming a complete closed-loop control loop, so that the coal feeder The speed is stable at the user's required setpoint. Another way through the power board shaping (opto-isolation) circuit, to the computer processor, the actual measured feed rate signal through the frequency / current conversion board (F / I) converted to 4 ~ 20mA current signal feedback to the user.
Third, the frequency conversion transformation program 1. The advantages of frequency control (1) frequency control energy, reduce consumption, high efficiency, power factor up to 0.98.
(2) Realize the soft start of the motor from 0r/min, no start impulse current, thus prolonging the service life of the motor.
(3) Inverter has a wide speed range, high control accuracy (up to 0.01Hz), stable speed and high reliability, low operation failure rate, and low maintenance.
(4) Complete protection function, with over-voltage, over-current, phase loss, under-voltage, short-circuit, locked-rotor, overheating and other comprehensive protection functions, and can display current, frequency, speed, shaft power, fault alarm and so on.
2. Renovation plan Replace the original slip speed control motor with the ordinary three-phase AC asynchronous motor of equal power, replace the original motor speed controller with the inverter, and the user is the same as in the past, that is, operation, calibration and degree of The method does not change.
(1) Speed-adjusting command signal input circuit Generally, the speed control signal of the inverter is 0-10VDC voltage signal or 0-20mA current signal, and the original microcomputer control board can not provide the above-mentioned analog signal, which needs to be in the microcomputer controller and The frequency converter/converter (F/V) is redesigned between the inverters to realize the signal connection between the microcomputer control board and the inverter. That is, the 30-1500Hz/10VDC pulse signal is converted into a 0-10 VDC analog signal, which is used as the input signal of the inverter's speed command. Input signal conversion circuit shown in Figure 2.
(2) Speed ​​feedback signal output circuit A non-contact speed measuring device—Hall sensor switch—is installed at the non-drive end of the motor. The device is reliable in operation, excellent in operating characteristics, and responsive and lossless. It takes 12 signals every rotation to replace the original AC tachometer generator and complete the closed-loop control.
In order to realize this speed feedback method, a signal conversion circuit needs to be established between the power board and the Zero sensor that collects the actual speed signal (12 sampling points/rev). The signal collected by the sensor is converted into a pulse signal of 0-300Hz (corresponding to 0-1500r/min) through this circuit, and sent to a microcomputer controller as a PID adjustment speed control signal through a power board shaping circuit to form a complete closed loop control loop. The speed of the coal feeder is stabilized at a given value requested by the user, and the actually measured coal feed rate signal is converted into a 4-20 mA current signal through a frequency/current conversion board (F/I) and fed back to the user. Speed ​​signal conversion circuit shown in Figure 3.
3. Commissioning of the speed control command signal input loop and speed feedback signal loop After the completion of the transformation, in the overall debugging, through the simulation of the coal drive under various operating conditions, the indicators are better than the slip speed motor Fully able to meet the needs of the unit to coal, to achieve the STOCK company type 8424 electronic weighing coal feeder from the slip speed to the frequency conversion speed control upgrade, and the user in the same as in the past, operation, calibration and determination The degree has not changed. Frequency conversion after the control block diagram shown in Figure 4.
IV. Conclusions 1. Improvement of safety and reliability After frequency conversion, because the frequency conversion control cabinet and motor are fully enclosed, the operating environment will no longer affect the safe and stable operation of the equipment and achieve the intended purpose.
As the low-voltage frequency conversion technology has matured in recent years, and the frequency conversion speed regulation has many advantages, so our factory frequency conversion speed-controlled coal feed motor has been put into operation since November 13, 2002, and the operating operators consistently reflect the operation of the coal feeder. Stable, stable speed, start and stop freely, can fully meet the needs of the unit to the coal, operating reliability has greatly improved.
2. Significant savings in energy consumption (1) Direct benefits The daily energy consumption (average) of the unit in various operating conditions, slip difference and frequency conversion is shown in Table 1.
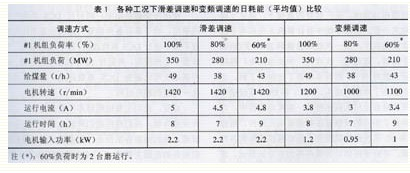
Energy-saving calculation:
◠Day saving power of one coal feeder: 8×(2.2-1.2)+7×(2.2-0.95)+9×(2.2-1)=27.55kWh
◠Calculated by the annual operating time of 7000h, the annual saving of electricity: 7000×27.55÷24=8035kWh
◠There are 24 sets of coal feeders of the same model in all 4 sets of the whole plant. If all of them are changed to variable-frequency adjustable-speed motors, the annual power saving will be 8035×24=192840kWh.
It can be seen that the economic benefits are considerable.
(2) Indirect benefits As the motor achieves a soft start from 0r/min, there is no start-up inrush current, thus extending the life of the motor. The overhaul and maintenance of the motor are greatly reduced compared with those before the transformation, greatly reducing the labor intensity of operation and maintenance personnel and improving the equipment operation and management level.
The use of domestic ordinary three-phase AC asynchronous motors to replace imported slip speed motors not only saves the purchase of imported spare parts for foreign exchange (about 55,000 yuan RMB), but also eliminates the 6-month long-term cycle required to order imported spare parts. The economic benefits are self-evident.
First, the existing problems (1) slip speed motor is to adjust the electromagnetic slip clutch coil excitation coil current to achieve speed control function, in which the speed excitation coil current loss of heat converted and the clutch master and slave rotor The heat generated by coupling in a magnetic field is cooled by natural wind. Due to the large dust in its operating environment, the air gaps between the clutch master and slave rotors are filled with ash. This can easily cause the slip motor to fail to adjust speed or fail to regulate speed. The amount of coal fluctuates greatly, causing it to be forced out of operation.
(2) The input speed feedback of the gearbox of the coal feeder is provided by the AC tachometer generator installed on the output shaft of the electromagnetic slip clutch. The magnetic rotor of the AC tachometer generator is easily damaged due to the material being brittle, resulting in The velocity feedback disappeared, the coal feeder tripped, and even the robbed coal machine jumped, thereby threatening the safe and stable operation of the unit.
According to incomplete statistics, Huaneng Shang'an Power Plant's Phase 1 2×350MW unit has been put into production since 1989. During the operation, the slippage of the 2×350MW unit has failed and the speed feedback has failed. As a result, the coal feeder has tripped and even jumped to the coal mill for more than 10 times.
Second, the 8424 type electronic weighing coal feeder control principle STOCK Corporation 8424 electronic weighing coal feeder control block diagram shown in Figure 1. The function of the power board is to convert the DC power of the user (DCS) to a low voltage stable DC power supply required for operating the electronic control equipment. The AC power is converted by the transformer into a series of low voltage power, and then is rectified, filtered and stabilized to supply the electronic power. Circuit use.
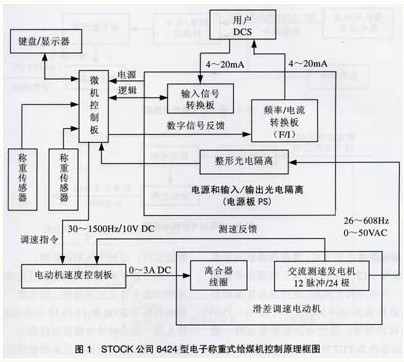
When the microcomputer control board receives the coal feeding rate request signal provided by the user (DCS) through the input signal conversion board, it measures the weighing signal and calculates and sends a speed control signal (30 to 1500 Hz/10 VDC) to the motor speed control board. . The motor speed control board can control the speed of the motor by controlling the amount of current that is input to the slip ring of the slip speed regulating motor, thereby driving the slip speed regulating motor to rotate to achieve the required speed.
The speed feedback of the slip speed regulating motor is a pulse signal sent from the AC tachometer generator installed on the output shaft of the clutch. All the way back to the summing point of the error amplifier of the motor speed control board, where the input signal is compared, the error amplifier to adjust the electromagnetic clutch coil current, to maximize the correction of the speed error, forming a complete closed-loop control loop, so that the coal feeder The speed is stable at the user's required setpoint. Another way through the power board shaping (opto-isolation) circuit, to the computer processor, the actual measured feed rate signal through the frequency / current conversion board (F / I) converted to 4 ~ 20mA current signal feedback to the user.
Third, the frequency conversion transformation program 1. The advantages of frequency control (1) frequency control energy, reduce consumption, high efficiency, power factor up to 0.98.
(2) Realize the soft start of the motor from 0r/min, no start impulse current, thus prolonging the service life of the motor.
(3) Inverter has a wide speed range, high control accuracy (up to 0.01Hz), stable speed and high reliability, low operation failure rate, and low maintenance.
(4) Complete protection function, with over-voltage, over-current, phase loss, under-voltage, short-circuit, locked-rotor, overheating and other comprehensive protection functions, and can display current, frequency, speed, shaft power, fault alarm and so on.
2. Renovation plan Replace the original slip speed control motor with the ordinary three-phase AC asynchronous motor of equal power, replace the original motor speed controller with the inverter, and the user is the same as in the past, that is, operation, calibration and degree of The method does not change.
(1) Speed-adjusting command signal input circuit Generally, the speed control signal of the inverter is 0-10VDC voltage signal or 0-20mA current signal, and the original microcomputer control board can not provide the above-mentioned analog signal, which needs to be in the microcomputer controller and The frequency converter/converter (F/V) is redesigned between the inverters to realize the signal connection between the microcomputer control board and the inverter. That is, the 30-1500Hz/10VDC pulse signal is converted into a 0-10 VDC analog signal, which is used as the input signal of the inverter's speed command. Input signal conversion circuit shown in Figure 2.
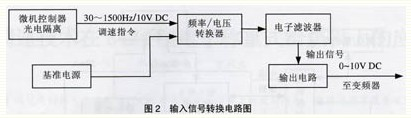
In order to realize this speed feedback method, a signal conversion circuit needs to be established between the power board and the Zero sensor that collects the actual speed signal (12 sampling points/rev). The signal collected by the sensor is converted into a pulse signal of 0-300Hz (corresponding to 0-1500r/min) through this circuit, and sent to a microcomputer controller as a PID adjustment speed control signal through a power board shaping circuit to form a complete closed loop control loop. The speed of the coal feeder is stabilized at a given value requested by the user, and the actually measured coal feed rate signal is converted into a 4-20 mA current signal through a frequency/current conversion board (F/I) and fed back to the user. Speed ​​signal conversion circuit shown in Figure 3.
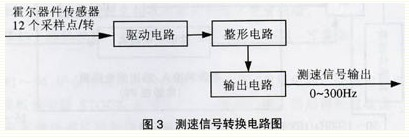
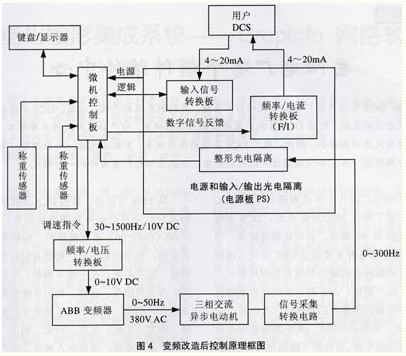
As the low-voltage frequency conversion technology has matured in recent years, and the frequency conversion speed regulation has many advantages, so our factory frequency conversion speed-controlled coal feed motor has been put into operation since November 13, 2002, and the operating operators consistently reflect the operation of the coal feeder. Stable, stable speed, start and stop freely, can fully meet the needs of the unit to the coal, operating reliability has greatly improved.
2. Significant savings in energy consumption (1) Direct benefits The daily energy consumption (average) of the unit in various operating conditions, slip difference and frequency conversion is shown in Table 1.
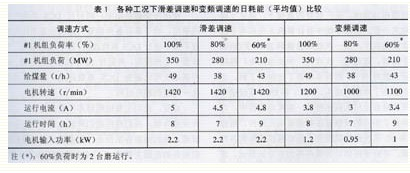
Energy-saving calculation:
◠Day saving power of one coal feeder: 8×(2.2-1.2)+7×(2.2-0.95)+9×(2.2-1)=27.55kWh
◠Calculated by the annual operating time of 7000h, the annual saving of electricity: 7000×27.55÷24=8035kWh
◠There are 24 sets of coal feeders of the same model in all 4 sets of the whole plant. If all of them are changed to variable-frequency adjustable-speed motors, the annual power saving will be 8035×24=192840kWh.
It can be seen that the economic benefits are considerable.
(2) Indirect benefits As the motor achieves a soft start from 0r/min, there is no start-up inrush current, thus extending the life of the motor. The overhaul and maintenance of the motor are greatly reduced compared with those before the transformation, greatly reducing the labor intensity of operation and maintenance personnel and improving the equipment operation and management level.
The use of domestic ordinary three-phase AC asynchronous motors to replace imported slip speed motors not only saves the purchase of imported spare parts for foreign exchange (about 55,000 yuan RMB), but also eliminates the 6-month long-term cycle required to order imported spare parts. The economic benefits are self-evident.
Auger Filler,Liquid Filling Machine,Tobacco Filling Machine,Juice Filling Machine
Wuxi Mingyan Equipment Co., Ltd , https://www.wxmyzbgroup.com