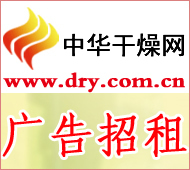
The special wax workshop of Henan Oilfield Refined Wax Factory has tapped the energy saving potential of the device. The workshop started by perfecting the daily supervision and inspection mechanism and carried out long-term operation and incentive mechanisms for equipment, prompting the employees of the team to strengthen the maintenance of equipment and energy-saving facilities and reduce the failure rate. At the same time, by analyzing the properties of raw materials and optimizing operating parameters, the temperature of the wax injection material is controlled to be 10-15° C. above the melting point, which effectively saves the amount of cooling water and steam. Through raw material configuration optimization and production plan adjustment, the raw material wax can be reused. Warming up or refining the white clay will reduce steam consumption, which in turn will reduce product energy consumption. In the first half of the year, the output of special wax blending devices increased by 3,840 tons year-on-year, while the overall energy consumption was reduced by 1.78 kg of standard oil/ton.
During this initial phase, Design Engineers, Tooling Engineers, Materials Engineers, Manufacturing Engineers, Quality Engineers, and Lab Technicians work together to determine product specifications, tooling component capabilities, tooling materials, operating limitations, and any required product enhancements and improvements. The team specifically looked for any potential issues with part geometry or tolerances that could result in poor steel condition or require special tool features such as lifters, slides and threading/unthreading. The physical and chemical properties of the selected resins are also evaluated in order to select suitable mold steels and review mold cooling. In addition to determining the proper vent location, a mold flow evaluation is performed to determine the optimal gate type and gate location.
The manufacturability review includes the validation of standard plastic design practices and the incorporation of tooling details to create the most robust design possible. Tool specifications and tool provenance are finalized and purchased component sources are qualified. A comprehensive Process Failure Mode Effects Analysis (PFMEA) was also completed.
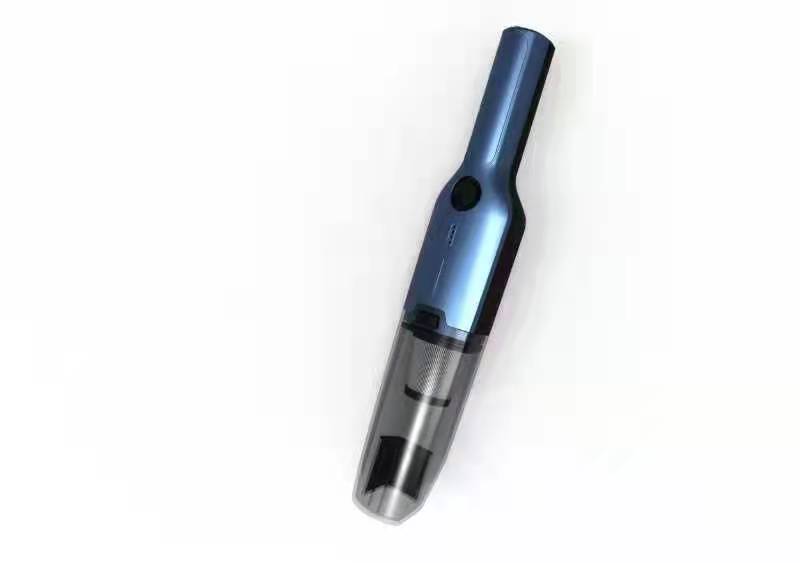
Automobile Plastic Parts,Plastic Injection Molded Automotive Parts,High Precision Abs Injection Plastic Molded Parts,Custom Injection Molded Plastic Abs Parts
Suzhou Dongye Precision Molding Co.,Ltd. , https://www.sjinjectionmolding.com