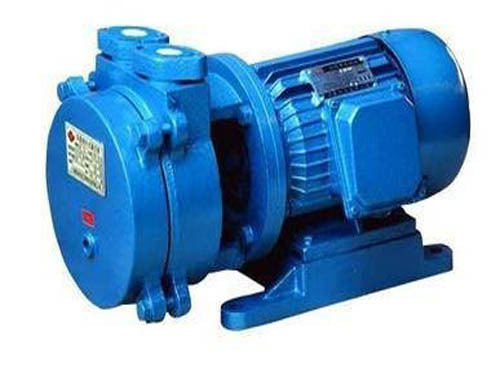
Water ring vacuum pump (referred to as water ring pump) is one of the water pumps, belonging to the ultimate vacuum it can obtain is 2000-4000Pa, and the serial air ejector can reach 270-670Pa. Water ring vacuum pumps can also be used as compressors, known as water ring compressors, which are low pressure compressors with a pressure range of 1 to 2 x 105 Pa gauge pressure.
The water ring vacuum pump has his unique features: compact structure, reliable work balance and uniform flow, and is mostly used in chemical production to transport or pump flammable, explosive and corrosive gases. The water ring type vacuum pump has low efficiency since the impeller stirs the liquid and loses much energy.
advantage
The structure is simple, the manufacturing precision is not high, and it is easy to process.
Compact structure, high rotation speed of the pump, generally can be directly connected with the motor, no need to reduce the device. Therefore, with a small structure size, a large displacement can be obtained, and the footprint is also small.
The compressed gas is essentially isothermal, ie the process temperature of the compressed gas changes very little.
Because there is no metal friction surface in the pump chamber, it is not necessary to lubricate the pump and the wear is small. The seal between the rotating part and the fixing part can be done directly by the water seal.
Inhale evenly, stable and reliable work, simple operation, easy maintenance.
Shortcomings
Low efficiency, generally around 30%, better up to 50%.
The degree of vacuum is low, not only because of structural restrictions, but more importantly because of the saturated vapor pressure of the working fluid. Water as the working fluid, the ultimate pressure can only reach 2000 ~ 4000Pa. With oil as working fluid, up to 130Pa.
In short, since the gas compression in the water ring pump is isothermal, flammable and explosive gases can be extracted. Because there are no exhaust valves and friction surfaces, dusty gases, condensable gases, and gas-water mixtures can be removed. With these outstanding characteristics, despite its low efficiency, it has been widely used.
Warp Knitting Machine Spare Parts
Warp knitting machines are used for the production of high-quality fabrics with intricate designs. These machines require various spare parts to ensure smooth and efficient operation. Here are some of the most common Warp Knitting Machine spare parts and their applications:
1. Needles: Needles are one of the most critical spare parts of a warp knitting machine. They are used to form the loops that create the fabric. Needles come in different sizes and shapes, depending on the type of fabric being produced, e.g., compound needle, slider needle, guide needle, threading comb and so on.
2. Sinkers: Sinkers are used to hold the fabric down as the needles form the loops. They come in different shapes and sizes and are made of various materials, including steel and plastic.
3. Guide bars: Guide bars are used to control the movement of the yarn as it is fed into the machine. They are available in different configurations, depending on the desired fabric design.
4. Electronic components: Modern warp knitting machines often require electronic components such as sensors, controllers, motors and EBC/EL device. These parts help to automate the machine and improve its efficiency.
5. Others like Piezo Jacquard, Warp Knitting Bellow, KFD tension device are also important to the machines.
In conclusion, warp knitting machine spare parts are essential for the smooth operation of these machines. They come in various shapes, sizes, and materials, and their selection depends on the type of fabric being produced and the machine's design.
Warp Knitting Machine Spare Parts
suzhou cotex international Co.,Ltd , https://www.macanol.com