-40ºF PDP 5% Purge Air 3.8m3/min Desiccant Air Dryer |
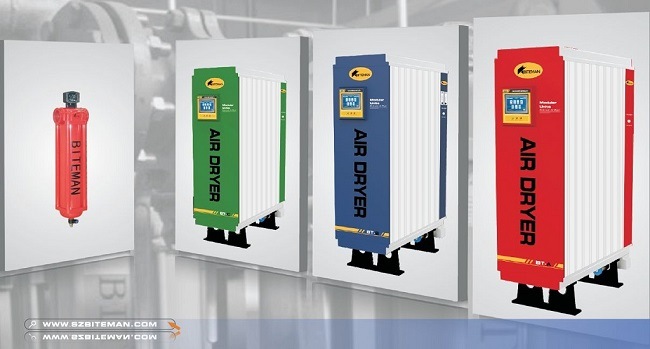
Features
1. Less than 5% purge air without auxiliary equipment, 012KW power consumption 2. Pressure and inlet temperature is digital readout on screen; purge air gauge allows manually control regeneration air according to the wanted pressure dew point 3. Small desiccant chambers' group, each chamber unit is independent and detachable 4. Replace with factory filled desiccant chamber, ease of maintenance and constant pressure dew point -40ºC (-40ºF) is ensured 5. The lowest operation cost, user could recoup dryer investment in three years by saving huge air and electricity 6. 1/3 size to traditional dryer 7. The shortest downtime 8. Using Molecular sieve as desiccant |
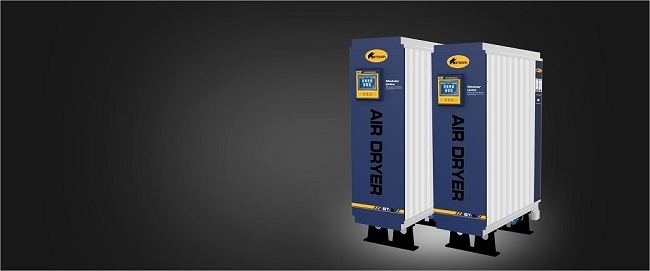
How it works
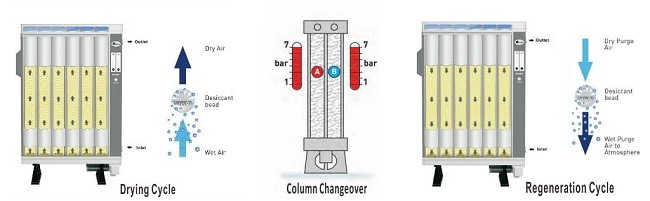
Drying cycle
The process air enters the dryer through the inlet and is directed into the on-line drying chamber via the inlet valves and lower manifold. The air is evenly distributed through the drying units and passes over the desiccant material, reducing the water vapour content. The dried process air then combines in the upper manifold and exits the dryer via the outlet check valves |
Column changeover
Before the on-line (drying) and off-line (regenerating) columns change over, the dryer exhaust valve, is closed, allowing the purge air to re-pressurise the off-line columns. This ensures a consistent system pressure and dewpoint when the drying chambers change over. |
Regeneration cycle
At the start of the regeneration cycle, the exhaust valve of the dryer is closed and the off-line chamber is at full line pressure. The air in the off-line chamber has a dewpoint equal to the air leaving the dryer. The exhaust valve is then opened and the dry air within the chamber expands rapidly as it leaves the dryer via the exhaust silencer, forcing water to be removed from the desiccant material. Once the off-line chamber has de-pressurised, a continuous bleed of dried process air is directed into the off-line upper manifold. This air is known as purge air. With the exhaust valve open, the purge air expands from line pressure to atmospheric pressure and flows downwards through the columns, over the off-line desiccant material. As the purge air at line pressure contains a fixed amount of water vapour, allowing it to expand means the purge air becomes even drier, increasing its capacity to remove water from the saturated desiccant bed. |
Details of advantages
Innovative structure with patents, adopts small desiccant chamber unit  1. Air flow equally and evenly pass through each desiccant chamber 2. Avoid channeling effect which more likely happens in traditional desiccant dryer 3. Small chamber allow no pressure vessel annul inspection 4. Molecular sieve capability is much better than Alumina and silicon desiccant in traditional dryer 5. Easy to maintain and replace factory filled desiccant chamber unit, ensure good performance as beginning 6. PLC controller, Full function touch panel control |
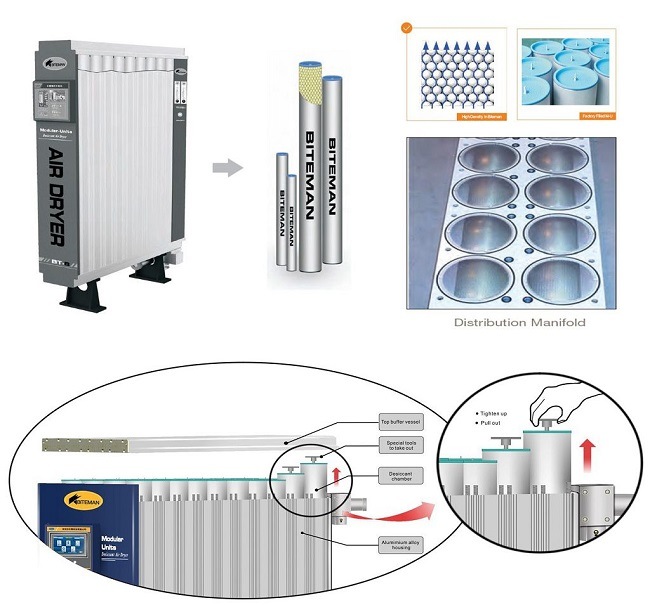
Product details
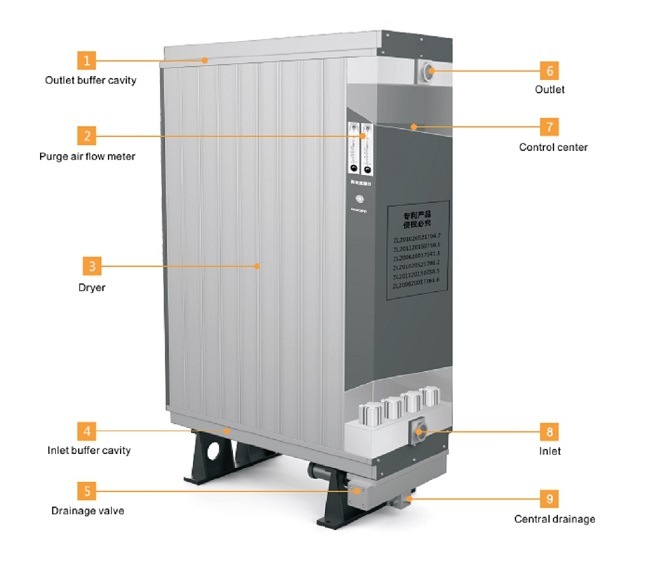
Specification data
BTGMXW-B Series | Heatless | |||||||
Model | Pipe Size (inch) | Flow Range(m³/min) | Dimension(mm) | Weight(kg) | ||||
@5~6bar | @6~7bar | @7~10bar | L | W | H | |||
BTGMXW015-B | G1 | 1.1 | 1.3 | 1.5 | 380 | 240 | 828 | 78 |
BTGMXW026-B | G1 | 1.9 | 2.3 | 2.6 | 380 | 240 | 978 | 87 |
BTGMXW038-B | G1 | 2.7 | 3.3 | 3.8 | 486 | 240 | 978 | 106 |
BTGMXW065-B | G2 | 4.8 | 5.8 | 6.5 | 486 | 240 | 1628 | 159 |
BTGMXW085-B | G2 | 6 | 7.4 | 8.5 | 595 | 240 | 1628 | 192 |
BTGMXW106-B | G2 | 7.4 | 9.1 | 10.6 | 703 | 240 | 1628 | 226 |
BTGMXW146-B | G2 | 9.8 | 12 | 14.6 | 920 | 240 | 1628 | 293 |
BTGMXW165-B | G2 | 11.6 | 14.2 | 16.5 | 1029 | 240 | 1628 | 327 |
BTGMXW206-B | G3 | 14.6 | 17.8 | 20.6 | 1250 | 240 | 1628 | 380 |
BTGMXW248-B | G3 | 16.7 | 20.5 | 24.8 | 829 | 480 | 1628 | 510 |
BTGMXW295-B | G3 | 21.5 | 26.3 | 29.5 | 938 | 480 | 1628 | 574 |
BTGMXW336-B | G3 | 24.1 | 29.5 | 33.6 | 1047 | 480 | 1628 | 638 |
BTGMXW385-B | G3 | 26.8 | 32.8 | 38.5 | 1156 | 480 | 1628 | 702 |
BTGMXW425-B | G3 | 29.7 | 36.4 | 42.5 | 1265 | 480 | 1628 | 767 |
BTGMXW465-B | G4 | 32.7 | 40.1 | 46.5 | 1374 | 480 | 1628 | 831 |
Installation
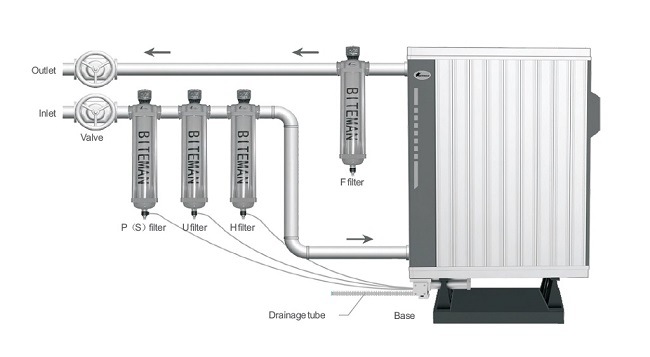
About Biteman technology
Biteman technology, the leading supplier and manufacturer of high efficiency desiccant air dryer and filter in China, with the advantages in low consistence PDP -40ºF, high efficiency 5% purge air, and easy to maintain, has widely applied for GM/P&G/Gree/BYD all over the world.  Contact us today to learn more. www.bitemantech.com |
Â
NPT hydraulic adapters are a type of hydraulic fitting used to connect hoses, pipes, and other components in hydraulic systems. NPT stands for National Pipe Taper, which is a U.S. standard for tapered pipe threads used on threaded pipes and fittings.
NPT hydraulic adapters come in different sizes and configurations to fit various hydraulic system components. They can be made of different materials such as brass, steel, or stainless steel, depending on the application.
These adapters are used to connect hydraulic components with different thread types or sizes, or to convert between straight and angled fittings. They have tapered threads that create a tight seal when tightened, ensuring that hydraulic fluid does not leak out.
When selecting NPT hydraulic adapters, it is important to choose the correct size and thread type for the hydraulic components being connected. It is also important to use the appropriate torque when tightening the fittings to prevent leaks and ensure a secure connection.
Metric To Npt Pipe Thread Adapter Factories,Metric To Npt Pipe Thread Adapter Manufacturers,Metric To Npt Pipe Thread Adapter,Metric To Npt Adapter Factories,Female Jic To Female Npt Adapter Factories
Zhejiang Hanying Technology Co., Ltd. , https://www.hydraulicfactory.com