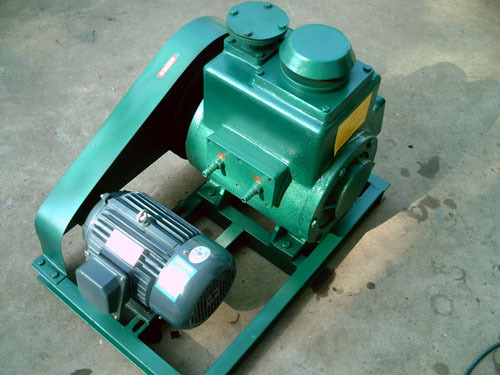
Fixed-plate vacuum pumps are used not only as pre-stage pumps for diffusion pumps or condensate pumps, but also for vacuum depressurization, dry distillation and the like. Fixed vacuum pumps feature simple structure, long service life, and easy maintenance.
Under normal circumstances, a vacuum pump of a general structure is not suitable for pumping a gas containing a large amount of water vapor, because the vapor will condense during the compression process, and because the pressure reached in the compression chamber gradually increases to the saturated vapor pressure (the operation of the pump At a temperature of about 60°C and a saturated vapor pressure of 150 mmHg), the vapor starts to condense. At this time, the exhaust valve has not been opened, so the vapor is not discharged. At this time, the vapor condenses into water in the pump and mixes with the oil. Stay in the pump together. After the water is mixed into the oil, it forms an emulsion. The oil contains acid, which causes gelation of the oil and oxidation of the metal parts of the pump, thereby damaging the mechanical pump. Sometimes the condensed water circulates with the oil in the aspirator. When it reaches the inlet end, it will cause re-evaporation and it will enter the pumped container, which will destroy the vacuum of the pumped container. Fixed-type mechanical pumps are characterized by simple structure, long service life, and easy maintenance. However, when the volume is large (ie, the pumping rate is required to be large), it is rarely used because the slide plate is difficult to ensure the seal.
With the development of the market, the fixed-plate vacuum pump itself is constantly improving. Because of its long service life, simple overhaul, convenient operation, etc., its share in the entire market is still very considerable because of its shortcomings. For professionals, there is room for development and improvement. The level of industrial production in our country is constantly improving, and how the fixed-plate mechanical pump embodies its value here, pending more research and innovation.
Granulator is mainly composed of feeding, mixing, pelletizing, transmission and lubrication system. Its working process is to require powder with water content less than 15%. It enters the feeding winch from the hopper. By adjusting the speed of stepless speed regulating motor, it obtains the appropriate material flow rate. Then it enters the agitator. It is conditioned by stirring and mixing with steam through the stirring rod. If molasses or grease need to be added, it is also added from the stirring barrel. When steam is tempered together, the amount of oil added is generally not more than 3%, otherwise it is difficult to form. After tempering, the temperature and humidity of the powder can reach 64-85 C and 14-l 6%. Then the iron impurities mixed in the powder are removed through the inclined groove through an optional iron absorption device, and finally the granulation is carried out in the pressing chamber.
Scope of use
1. Pelletizer is a kind of swing action of rotating drum. It can grind wet powder materials into granules through wire sieve, and it can also be widely used to crush the granules that have become blocks and become ready-made granules.
2. In chemical medicine, it is used to grind wet powders into granules, dry them for pressing tablets, crush the caked cakes during storage or during chemical processing, treat confectionery and sugar mixtures, malt milk and other products in food industry, and mix ceramics and plastics in other industries. The mixture becomes the molding granule.
3. it is not suitable for semi-solid, fluid, slurry or wear.
CHANGZHOU
SULI DRYING EQUIPMENT CO.,LTD.specializing in the production of Mixing
Dryer, Spray Dryer, Granulation Dryer ,Crushing Dryer, 3D Motion Mixer
and V-shaped Mixer.
Granulator Series,Fluidized Granulator,Bed Granulator Machine,Swinging Granulator
Changzhou Su Li drying equipment Co., Ltd. , http://www.sldrying.com