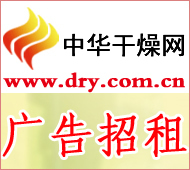
At the 2012 China (Changshu) International Fluorine Chemical Industry Forum sponsored by the China Petroleum and Chemical Industry Federation on the 24th, Zhang Fang, Director of the Fine Chemicals Department of the Petroleum and Chemical Industry Planning Institute, disclosed that a copy of this book was written by the Institute. The draft of the Fluorinated Industrial Policy has been submitted to the Ministry of Industry and Information Technology. It has entered the internal and inter-ministerial revision and signature stage and is expected to be released at the end of this year. Analysts believe that the policy will further strict access, reverse vicious competition, will have a positive impact on leading enterprises.
It was learned from the industry that this "Fluid Chemical Industrial Policy" includes the policy objectives of promoting China's upgrading from the largest fluorinated industrial country to the largest fluorinated industrial country, the orientation of product structure adjustment, technical policy and raw material policy, and the implementation of international conventions related to fluorine chemicals. Requirements and other content.
Previously, the "hydrofluoric acid industry access conditions" was released in March last year, the new production company's total hydrogen fluoride should not be less than 50,000 tons / year, and should have a stable and reliable protection of fluorite resources. However, Zhang Fang stated that the above “Entry conditions†only targeted hydrogen fluoride species, and the “Fluid Chemical Industry Policy†was aimed at making stricter access regulations for almost all fluorine chemical products and proposed some new requirements. In terms of scale, key raw materials, comprehensive energy consumption and other aspects, some of the varieties are not only newly constructed, but also include restrictions on the expansion and expansion. At the same time, industrial policies have also made comprehensive provisions on the energy consumption, environmental protection, and import and export policies of upstream hydrofluoric acid. Wei Aihua, chairman of San Aifu, said yesterday that it is expected that by the end of the “Twelfth Five-Year Planâ€, China’s total fluorine chemical industry output value will reach 150 billion yuan, with an average annual growth rate of about 37%.
"Gravity Die Casting. A permanent mould casting process, where the molten metal is poured from a vessle of ladle into the mould, and cavity fills with no force other than gravity, in a similar manner to the production of sand castings, although filling cn be controlled by tilting the die."
Gravity Die Casting
Sometimes referred to as Permanent Mould, GDC is a repeatable casting process used for non-ferrous alloy parts, typically aluminium, Zinc and Copper Base alloys.
The process differs from HPDC in that Gravity- rather than high pressure- is used to fill the mould with the liquid alloy.
GDC is suited to medium to high volumes products and typically parts are of a heavier sections than HPDC, but thinner sections than sand casting.
There are three key stages in the process.
- The heated mould [Die or Tool] is coated with a die release agent. The release agent spray also has a secondary function in that it aids cooling of the mould face after the previous part has been removed from the die.
- Molten metal is poured into channels in the tool to allow the material to fill all the extremities of the mould cavity. The metal is either hand poured using steel ladles or dosed using mechanical methods. Typically, there is a mould [down sprue" that allows the alloy to enter the mould cavity from the lower part of the die, reducing the formation of turbulence and subsequent porosity and inclusions in the finished part.
- Once the part has cooled sufficiently, the die is opened, either manually or utilising mechanical methods.
Advantages
- Good dimensional accuracy
- Smoother cast surface finish than sand casting
- Improved mechanical properties compared to sand casting
- Thinner walls can be cast compared to sand casting
- Reverse draft internal pockets and forms can be cast in using preformed sand core inserts
- Steel pins and inserts can be cast in to the part
- Faster production times compared to other processes.
- Once the tolling is proven, the product quality is very repeatable.
- Outsourced Tooling setup costs can be lower than sand casting.
Gravity Casting Parts,Aluminum Alloy Gravity Casting Parts,Aluminum Gravity Die Casting Parts,Gravity Casting Aluminum Parts
HSI INDUSTRIEL LTD , https://www.hsiindustriel.com